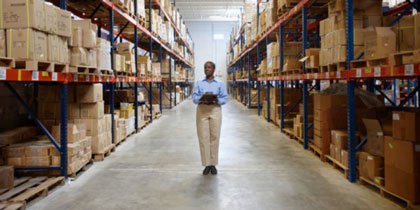
Although they are closely connected, transportation and finance often hold opposing views when it comes to transportation costs.
While the Finance department mainly focuses on ways to become more profitable, logistics managers are more interested in analyzing their department’s budgets and metrics.
This discourse often causes a lack of communication between the CFO and logistics managers.
To create a smoother transition of information and allow both departments to be on the same page, we recently looked at several key questions about logistics and transportation strategies as they relate to financial performance.
How much inventory should you carry?
While developing a leaner inventory is often a popular first move, data has shown that it has a negative impact on cost. A leaner inventory means faster transportation, which demands premium rates and may increase many other costs of operation.
To a CFO, lean inventory means reducing the working capital tied up in inventory. But to a logistics manager it means filling the need for expedited freight, dealing with complicated changes in transportation modes, and pressure for more accurate fulfillment.
Lower inventory can impact those involved in several ways, including higher freight costs, stock outs, and increased labor costs.
The bottom line is this: a reduction in inventory levels carries a high likelihood of an increase in costs, potentially negatively impacting your operating margins and diminishing revenue when you decide to decrease inventory.
To learn more about transportation’s impact on financial performance, we invite you to download the whitepaper The Freight to Finance Translation Guide: A CFO Primer on Transportation’s Impact on Financial Performance.